Book conservators treat volumes that vary in size, shape, and functionality. When treating the interior of a book, the binding often needs to be secured in an open position to give the conservator access to the text-block material (paper or parchment), media, or interior structure. We come up with all kinds of ad-hoc ways to hold books in the positions we need by using tools like wedges, weights, and ties. But not all books can safely open very far. Depending on the flexibility of the spine or the fragility of the paper, books sometimes need to be held open at a right or acute angle to avoid causing further damage, and this can make handling the book tricky.
In spring 2019, the Libraries’ conservation lab teamed up with a group of undergraduate students in the McCormick School of Engineering’s Design Thinking & Communication (DTC) course to design a tool that could solve this problem.
DTC is a required course for all engineering undergraduates. Student teams are paired with community partners who bring them design problems. The students then spend the quarter getting a sense of their partner’s problem and building mock-ups and prototypes to solve it.
We were partnered with two teams of students for our book support project. They came to the conservation lab several times throughout the quarter to learn about book conservation, to watch us work, and to hear our ideas and specifications for what we wanted. We gave them some sketches for what we had in mind for the tool, but we also told them they could take the design in any direction they wanted.

Design mock-ups made by the DTC students.
Throughout the quarter, the students periodically returned to the lab to show us mock-ups they were building, to ask us questions about use and functionality concepts, and to get our feedback. It was fascinating to see their different working styles and watch their ideas come to life.
At the end of the quarter, both groups presented their final prototypes. We really loved the outcome. One team stuck close to what we had sketched out, creating an engineering solution for the drawings we had provided. The other team took their design in a different direction, building an entirely new clamping system to hold the book in place.
We got to keep the prototypes and put them to use in our treatments. They worked well, but there were a few issues we wanted to resolve. We also wanted to replace the custom-made pieces incorporated into the design with prefabricated parts so other conservators could construct one of their own with purchased supplies.
After further prototyping, we have designed a working model for the tool, called the “Adaptable Conservation Book Support” (ACBS). Using all pre-made parts, the design is simple and inexpensive to construct. The tool can hold a wide range of books (varying in size and shape) open at any desired angle. The clamping mechanism is highly adaptable to meet any book’s needs (e.g., avoiding delicate media, photographs, or previous damage), and makes for easy page-turning when treating large portions of the text-block. The tool can also be useful for the digitization process during which books need to be held open for image capturing.

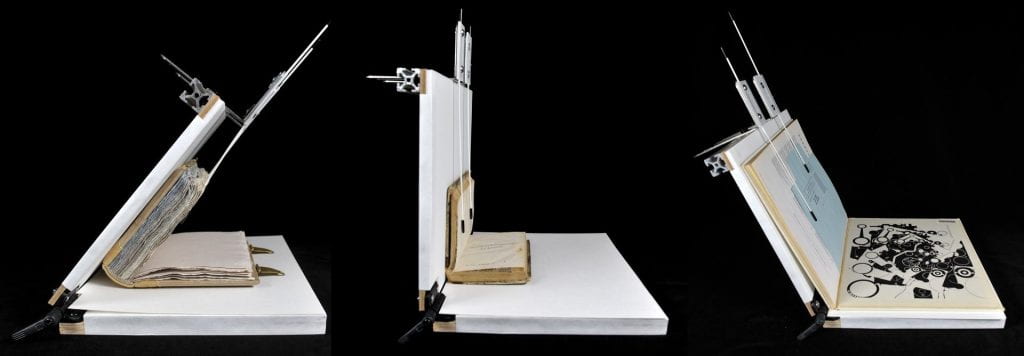
We have created a supplies list and assembly instructions that are shared on the American Institute for Conservation’s Wiki. The tool is intended to be both DIY and open-design, welcoming design suggestions from other conservation practitioners. Hear more about the ACBS in this webinar for the Institute of Conservation, a U.K.-based professional organization for cultural heritage conservators.
The ACBS has already begun to evolve. In July 2020, a team at the Auckland War Memorial Museum in New Zealand built their own ACBS and designed a set of 3D-printed parts that improve the functioning of the clamping system. They have made the printing files available for others hoping to make their own, continuing the collaborative nature of the tool. Check out this blog post about the project at the Auckland Museum.
It is exciting to have the opportunity to collaborate with colleagues on the other side of the world. And now the modifications made by the team in Auckland can be put to use by library professionals everywhere! We look forward to seeing this tool continue to evolve.

Auckland Museum Display Manager Heath King designed 3D-printed parts for the ACBS (photo: Nina Whittaker).

Paper Conservator Erin Walker working with an ACBS made at the Auckland Museum (photo: Nina Whittaker).